How to use metal wound gaskets in traditional mechanical equipment? When metal wound gaskets do not appear, most companies often use parchment paper pads or simply do not use them at all. For example, ordinary locomotive manufacturers, mainly in transmission. Sheepskin pads are required between the bearing seat and the flange of the wheelset. Mainly because parchment pads are easy to manufacture and inexpensive. However, the service life of the parchment paper pad is short. If the butter is sealed, the butter will usually dry out in more than a year. Usually, the general locomotive manufacturer chooses to carry out a comprehensive maintenance in about a year, that is, re-adding the butter. Although there are metal wound gaskets now, many locomotive experts still use parchment pads, or do not use them at all, mainly to save costs.
It may be possible to temporarily use paper pads or no pads on the bearing seat and flange of the locomotive, and there will be no problems in a short time. After a long time, it is necessary to re-maintain and re-fill oil. But can some industries with high sealing requirements also do the same? For example, in the petrochemical industry, can we avoid the use of metal spiral wound gaskets? Of course not. It should be known that many oil leakage accidents are caused by the problem of the flange, but the main source of the leakage problem is the problem of the metal wound gasket inside. Therefore, the flanges in power, ships, and pressure vessels must also use metal wound gaskets.
First, clean the sealing surface of the flange, and pre-assemble the wound gasket without removing the plastic packaging tape with the flange of the pipe box to ensure that the gasket is in place correctly, and install the stainless steel inner ring of the metal wound gasket with the pipe box method. The blue is equipped with the above 4 evenly distributed positioning holes. Then, carefully remove the plastic wrapping tape of the metal wound gasket and check that the gasket surface is free of defects such as radial scratches. Finally, fix the metal wound gasket to the flange of the tube box with elastic cylindrical pins, and then proceed to assemble the tube box assembly and the tube sheet.
Because there are positioning holes drilled on the inner ring of the metal wound gasket at the flange of the pipe box, if the equipment needs to be replaced at china Exhaust Muffler Gasket wholesale the customer site for maintenance or customer overhaul, the method described in this article can be used to replace the original elastic cylindrical pin and gasket. Take it off and drill pilot holes on the new metal wound pad, which will not have any effect on the installation at the customer's site.
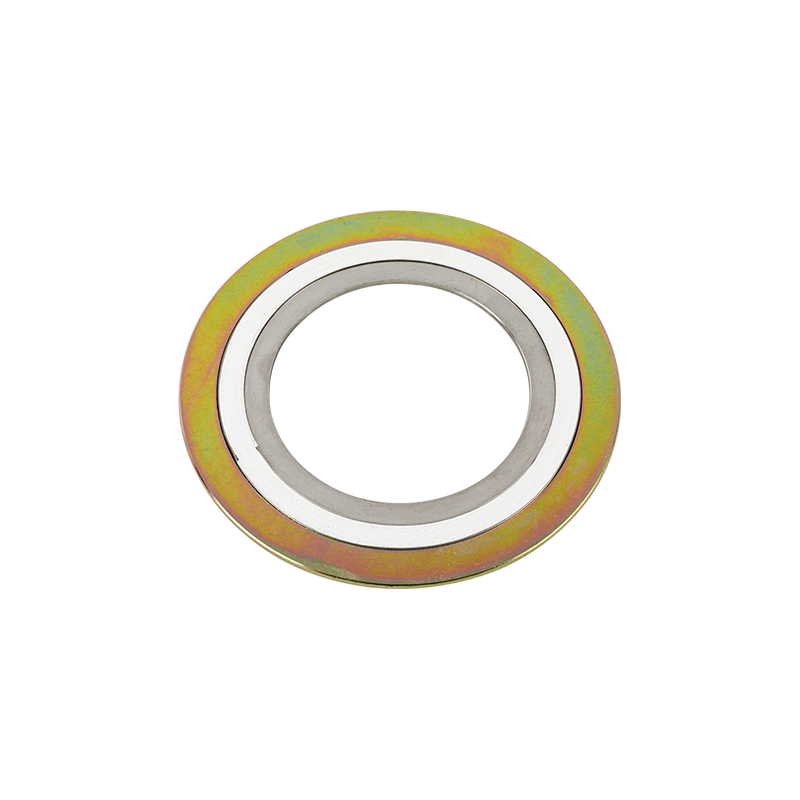
Correct and reliable installation of metal wound gasket is the key to ensure good sealing effect. For non-basic metal wound gaskets, there are usually two types with an inner ring or with an inner ring and a centering ring. The case of drilling a positioning hole in a metal wound gasket introduced in this article provides a guide for the installation of the metal wound gasket. New ideas, especially for large-diameter metal wound gaskets, while controlling the bolt tightening sequence and tightening torque are important factors to ensure the sealing of metal wound gaskets. It should be pointed out that for large-diameter metal spiral wound gaskets, the effect of internal pressure on the stress of the sealing metal spiral wound gasket will cause the bolt to stretch. Properly increasing the bolt tightening torque is an important factor to achieve long-term reliable sealing.